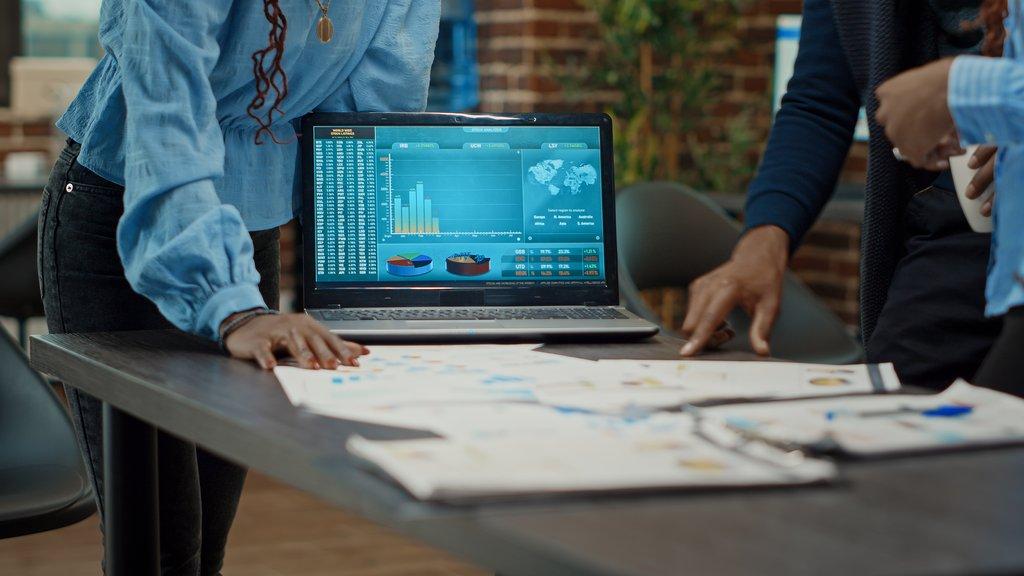
In today's dynamic manufacturing environment, businesses must manage growing customer expectations, rising operational costs, and increasingly complex supply chains. At the heart of overcoming these challenges is production planning—a process that ensures you’re making the right product, at the right time, using the right resources.
But production planning isn’t just about creating a schedule. It’s about synchronizing every aspect of operations: material availability, workforce capacity, machine readiness, procurement timing, and customer delivery. This is where traditional systems fall short and where ERPNext comes in—an intelligent, integrated ERP solution that brings end-to-end visibility and control to your production operations.
What is Production Planning?
Production planning is the process of determining how goods will be produced, when they will be produced, what resources are needed, and how they will flow through the production system. It serves as a bridge between sales forecasts or customer orders and the shop floor where products are made.
- What to produce?
- How much to produce?
- When to start and finish production?
- What raw materials, tools, and resources are needed?
- How will the process flow?
Done well, production planning enables manufacturers to reduce idle time, minimize waste, optimize capacity, ensure quality, and meet delivery deadlines without chaos.
Why Production Planning Matters More Than Ever
Modern production is no longer linear or predictable. With demand fluctuations, raw material delays, labor shortages, and custom product configurations, manufacturers must be agile and informed.
- Timely fulfillment of customer orders
- Optimized use of machines and labor
- Reduced production and inventory costs
- Shorter lead times
- Improved product quality
- Better responsiveness to market changes
- Enhanced profitability
Traditional vs. Modern Production Planning
Traditional planning used spreadsheets and separate systems, resulting in miscommunication and slow updates. Modern ERP-based planning, such as ERPNext, integrates all departments, offers real-time updates, and automates tasks for agility and accuracy.
Types of Production Planning Strategies
- Make to Stock (MTS): Produce based on forecast; used in high-volume industries.
- Make to Order (MTO): Begin production only after an order is received.
- Assemble to Order (ATO): Build components in advance; assemble after order.
- Engineer to Order (ETO): Custom-designed and built per order, common in project-based manufacturing.
Key Elements of Production Planning in ERPNext
1. Bill of Materials (BOM)
Defines materials and steps required for a product. ERPNext allows multi-level BOMs, version control, and linking inspections to ensure consistency and cost accuracy.
2. Routing and Operations
Maps the operations sequence (cutting, welding, etc.) and assigns workstations. Helps track estimated vs. actual time and improve shop floor flow.
3. Work Orders
Generated from Sales Orders, they trigger production and are updated through various statuses (Planned, In Progress, Completed). ERPNext links them with BOMs and tracks material usage and job progress.
4. Material Requirements Planning (MRP)
Automatically checks stock, forecasts material shortages, and creates purchase or transfer requests to avoid delays or excess stock.
5. Capacity Planning
Ensures machines and labor can handle the workload. ERPNext tracks utilization and recommends load balancing.
6. Job Cards & Shop Floor Control
Workers use Job Cards to log operation progress, scrap, and downtime. Managers gain real-time visibility into performance and bottlenecks.
7. Quality Checks
Inspections can be configured at any stage. ERPNext records results, links them to batches, and ensures compliance with specifications.
Real-Life Example: Garment Manufacturer
Before ERPNext: Disorganized work orders, delays, missed deliveries, overstocking.
After ERPNext: Automatic work orders, MRP for raw materials, real-time shop floor tracking, improved delivery rates and reduced waste.
Best Practices for Production Planning
- Update BOMs regularly
- Use demand forecasting for better accuracy
- Define realistic machine and shift capacities
- Standardize quality inspections
- Train operators for data entry on shop floor
- Monitor KPIs via dashboards
Conclusion
Production planning isn't just a manufacturing task—it's a strategic function that determines how well your business meets demand, controls costs, and delivers on time. ERPNext gives you the power to bring structure, accuracy, and agility to your production lifecycle. By integrating all elements of manufacturing into one platform, it helps you reduce chaos and plan smarter every step of the way.
No comments yet. Login to start a new discussion Start a new discussion